Food Safety
Inspection Solutions
After reading our eBook How to Get the Best Value from a Critical Control Point in Food Production you will know how to successfully implement an inspection system into your food production to ensure only the safest and highest of quality products are delivered to your customers.
The eBook explains what is expected from HACCP now and in the future, and why you too should inspect primary packaged products.
Fill in the form and you will receive the eBook to your inbox for free!
Check Weighing.
Is supplying correct weights to supermarkets and other clients a necessity? The EZI-Check™ inspection system is a new high speed in-line checkweigher that’s been specially designed to weigh, classify and segregate products based on weight. Its Japanese design provides high-level performance, accuracy and reliability, making it easily adaptable to existing lines.
This in motion checkweigher is versatile with dual range capacity and high repeatability. Great for applications in food & beverage and fresh fruits in clamshell packaging.
Speak to one of our consultants to determine if this is the right solution for you or we may suggest a better alternative.
Food Grade Metal Detectors.
Food grade metal detectors are essential to ensure the safety of your products. Metal detection is used to identify and remove metal contaminants from food products. They can be fitted in various locations: either in processing to protect processing equipment during production, can be fitted as part of the packaging process or after packaging and are essential in preventing contaminants with metal fragments from reaching processing equipment, protecting blades etc. or reaching consumers and endangering consumers.
Metal detectors work by generating a magnetic field and analysing the signals produced when metal is detected. If any metal is found, the system triggers an alarm or activates a rejection mechanism to remove the contaminated item. Food grade metal detectors are essential for manufacturing compliance with food safety regulations, and to maintain consumer trust.
Speak to one of our consultants to determine if this is the right solution for you or we may suggest a better alternative.
X-Ray Inspection.
Food Safety and Quality control are growing global trends. Many authorities, global retail chains, and even consumers demand better and consistent quality from the food products they buy. It is expected that food producers are aware of their safety risks and control them accordingly while maintaining the high quality of their food products.
This level of food safety and quality can be achieved by implementing food X-ray inspection system in your production line. By automating the quality and safety inspection with X-ray inspection systems, food producers can eliminate the risks of contamination due to human errors and improve the efficiency of their production line by inspecting for foreign objects and other quality defects simultaneously.
The X-ray inspection system inspects, detects, and automatically rejects hazardous foreign objects from your production line. At the same time, the system is able to inspect the overall quality by analyzing the content of the packaged product, such as:
Completeness and integrity
Form and shape
Presence and lack of presence
Fill level
These features of X-ray inspection systems are a huge benefit for food producers, who want to reach the highest level of product safety and quality. With the added traceability that X-ray inspection systems offer, food companies are also able to prove that their products were indeed safe and high quality when leaving the production facilities.
Speak to one of our consultants to determine if this is the right solution for you or we may suggest a better alternative.
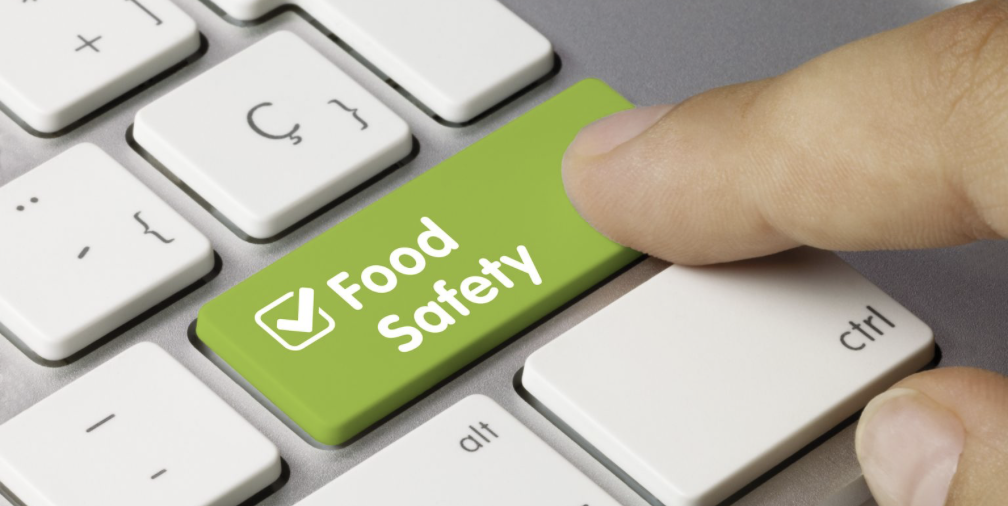